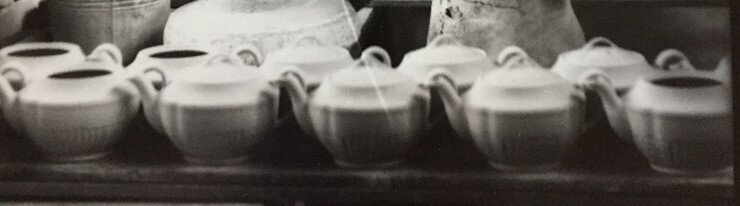
Making a Ceramic Teapot
Teapots were among the first items produced by East Liverpool’s nineteenth century potters. The Museum of Ceramics has extant yellowware and Rockingham teapots attributed to Bennett, Baggott, Croxall, Harker and other potters of the mid-1800s.
The teapots of that time were made from the locally mined, yellow clay. The buff-burning clays of the region, formed during the Pennsylvania Age (310-280 million years ago), are the lower Kittanning layer. The deposits range from eight to 15 feet in depth. Lower Kittanning clays contain fewer impurities than many other types and are well suited for production of dinnerware and toilet ware.
The spittoon pictured here is one of the earliest pieces produced in East Liverpool and is a fine example of yellowware. The local clay ranged in color from a pale buff to a bright yellow. No color or dyes were added to the clay. This spittoon bears a mark that was used by James Bennett, the first commercial potter of East Liverpool. Bennett’s pottery was in operation from 1840 to 1844.
“The Presser” an oil painting by WPA artist Roland Schweinsburg.
Museum of Ceramics Collection
To prepare the clay for shaping, the potters would first mix it with water in a blunger, creating slip or slurry. This liquid would pass through screens to remove any impurities. A filter press was used to remove excess water and a pug mill kneaded the clay and removed air bubbles.
It was then shaped in a mold. Early potters used a process called pressing. They would take the prepared clay and press it into a mold using their hands and special tools, such as a “jolly stick.” Seams were joined and smoothed and the thickness of the teapot walls were made uniform. After the clay dried, the molds were removed and spouts were added. Early teapot spouts had a small grate for catching tea leaves and it is because of this feature that the teapot could not be molded in one piece.
Another method, slip casting, is now the preferred procedure for commercial mass production. Slip is poured, rather than pressed, into a plaster mold. The plaster mold absorbs water from the clay and, after a specified drying time, the excess clay is poured out of the mold. Wikipedia describes it this way, “once the plaster has absorbed most of the liquid from the outside layer of clay the remaining slip is poured off for later use. After a period for further absorption of water, the cast piece is removed from the mold once it is leather-hard, that is, firm enough to handle without losing its shape. It is then ‘fettled’ (trimmed neatly) and allowed to dry out further, usually overnight or for several hours. This produces a greenware piece which is then ready to be decorated, glazed and fired in a kiln.”
The molds above are for the Sherlock Holmes teapot designed by Don Schreckengost and created by Hall China Company. The pot was commissioned by Dan Brasier in celebration of the 100th anniversary of the first publication of Sir Arthur Conan Doyle’s famous novel, A Study in Scarlet. Intricate teapots such as this one were made from several molds and then glued together with slip (liquid clay). The mold’s two pieces show the details of the front and back of Holmes’ hand. The body of the piece would be another mold, and yet another for the hat. Less detailed teapots could be made with two molds, one for body and one for lid. Brasier donated all of the molds and several Holmes teapots to the Museum in 2017.
In the photo on the right, Clyde McClellan, owner of American Mug & Stein pottery, East Liverpool, Ohio, explains the slip casting for making steins to a Clay Camp participant. (Clay Camp is a day camp, held by MoC for kids ages ten to 14). The molds and the slip hose can be seen in the lower portion of the photo.
The greenware (shaped but unfired) teapot would then be fired in a kiln. Today’s potteries use tunnel or continuous kilns. Nineteenth century potteries used bottle kilns or periodic kilns; they had to be unloaded after every firing. All ware was fired at least twice until Robert Hall Jr. of Hall China created a one fire method in 1911.
The bottle kiln shown here still stands in East Liverpool on Second Street. The potteries of Goodwin and Baggot operated here. Firemouths (openings seen near the bottom) were loaded with coal and fired; it took 15 tons of coal for one firing. Firing for bisque ware took three days. Temperatures rose slowly to dry the ware and then reached maximum temperature, about 2200 F after two days. Glost firings (for glazed ware) took two days and reached about 2000 F. Kilns would be unloaded 48 hours after the fires were out. Often companies urged quicker unloading, as early as 24 hours later, when kiln was still red hot. Men wore wet layers of clothing to guard against heat and wrapped their hands. Kiln working was hard and hazardous work.
After firing the bisque teapot would be glazed by hand-dipping and/or spraying and then fired again in a glost kiln. More often than not, yellowware teapots (and other ware) were coated with a brown manganese glaze known as Rockingham. This glaze was developed at the Swinton Pottery, Yorkshire, England, that stood on the property of the Marquis of Rockingham. American potters called this ware by various names, including brown ware, until James Bennet began calling it Rockingham. This led many to believe that he was the first to produce Rockingham in the United States which was not the case; he was simply the first to call it that. See the “Early Potters” Docent Chat for additional information and Gallery, “Early Teapots,” for examples of Rockingham teapots.
Just for fun:
This is not a video about East Liverpool area potteries. Instead, it is about the production of the “Brown Betty’ teapot which is still being made today in Stoke on Trent. Rather than yellow clay they use a red clay called Etruria marl and show it being extracted from the clay seam, processed at Valentine’s Clays, and molded by hand at Cauldon Ceramics, the oldest remaining maker of the Brown Betty teapot.
By the 1870s, Rockingham tableware was passé and consumer tastes dictated a more refined but elaborately decorated teapot. Teapots made using white clay were blank canvases for decorators and East Liverpool potters began importing clay to make the more delicate looking whiteware. This clay, unlike yellowware clay, is a combination of raw ingredients that are not available in East Liverpool. The ingredients include kaolin, known as china clay, feldspar, and flint (or silica). Once the teapot was decorated with decals, gold lining, transfer prints, hand painting or a combination of several of these techniques, it would be fired again to adhere the colors to the glaze. The photos below depict decorators: On the left is a woman from an unknown local pottery hand lining a teapot, most likely with gold. The small round table on which the pot sits is a “liner’s wheel” or a “whirler.” On the right is a photo taken at Hall China in 1937 and shows a potter holding the Bru-o-lator teapot, an example of which may be seen in Hall Gallery Two. (photo courtesy Clevelandmemory.org)
Where it all starts…
All teapots start with an idea that is made real by creating a physical model of the desired shape. In the nineteenth century, these models were created by hand by skilled artisans. Early potteries were small, often with only three or four employees who participated in every aspect of production. As the potteries grew, art departments were organized and this is where products were, and still are, designed. Technology has replaced the hand crafting of the model with computer generated designs that are printed in resin with a 3D printer. From this model, a plaster mold is created and another model is made…this time of plaster. The plaster model allows the creator to smooth out curves and remove any edges that the computer was unable to perfect. Once the model has been adjusted, another plaster mold is created and production begins.
Where it all ends…
It all ends in the home of the consumer. And the result is one of the most beautiful pieces of ware found in food service. The graceful curves of the tea server, the applied decorations, and the knowledge that it holds a delicious steamy treat make it irresistible to tea drinkers and collectors. This exhibit features over 250 Crockery City Teapots. Visit the Galleries and marvel at the artistry.
The content of this essay is from the exhibit script for the Museum of Ceramics.
Special thanks to Mick Bowdler for providing information about the design processes.